The Critical Role of a Lathe Parts Factory in Modern Manufacturing
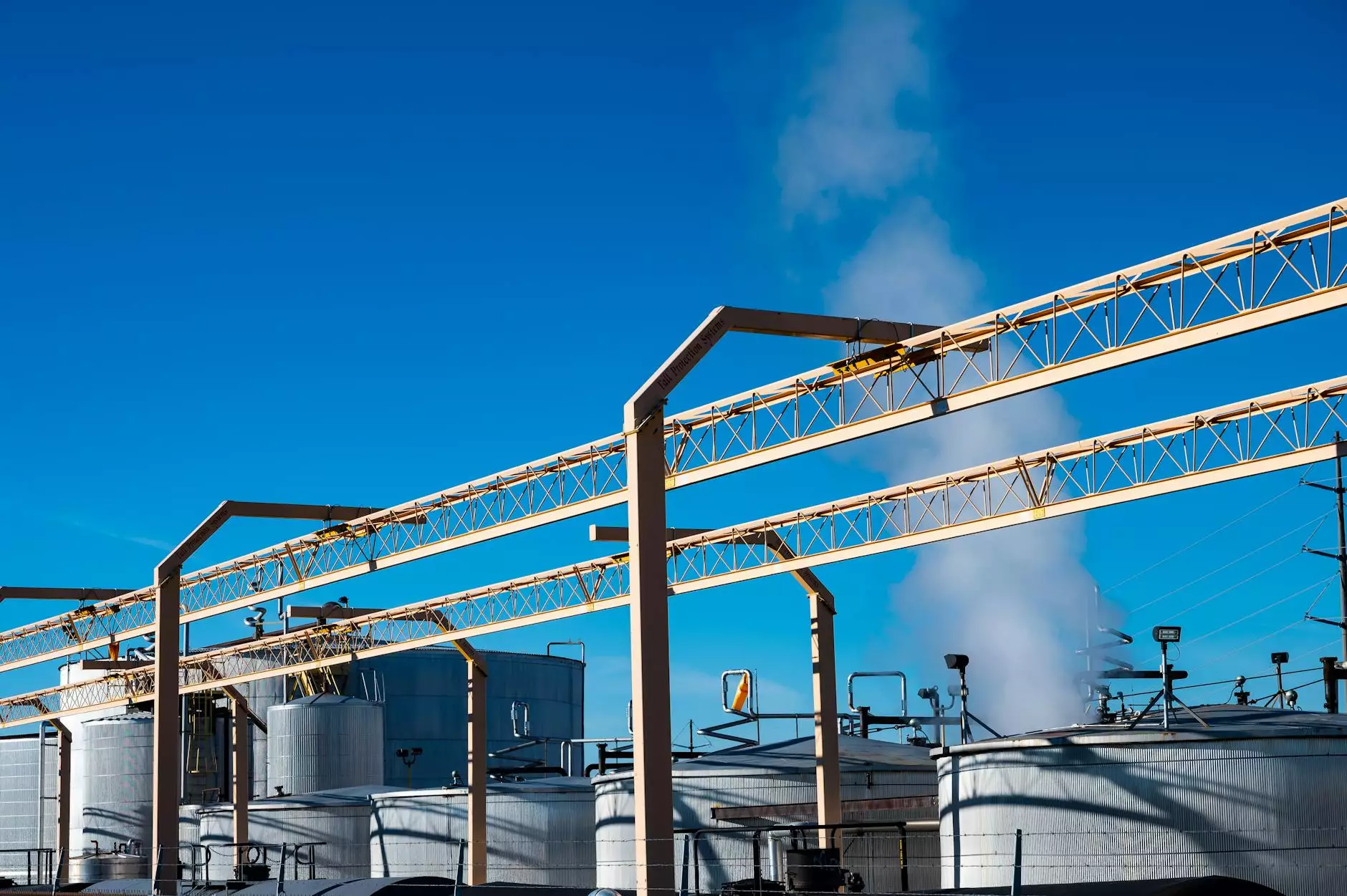
The manufacturing industry today is driven by precision, efficiency, and adaptability. One of the key players in this dynamic field is a lathe parts factory. These factories are essential to the production of an array of components used across various sectors, from aerospace to automotive. This article delves deeply into the significance, functioning, and technological advancements pertaining to lathe parts factories, highlighting why they are indispensable in contemporary manufacturing setups.
Understanding the Basics: What is a Lathe Parts Factory?
A lathe parts factory specializes in the production and supply of components manufactured primarily through the lathe machining process. This includes a diverse range of parts, such as:
- Shafts: Essential for transmitting power in machinery.
- Brackets: Used for mounting and securing equipment.
- Housing: Protects machinery and ensures safety.
- Spindles: Crucial for rotary motion in various machines.
- Custom parts: Tailored to meet specific client requirements.
The Process of Manufacturing in a Lathe Parts Factory
The manufacturing process in a lathe parts factory involves several critical steps designed to ensure quality and precision.
1. Design and Blueprint Creation
Every successful part begins with a detailed design. Engineers and designers use CAD (Computer-Aided Design) software to create accurate blueprints that serve as essential guides during the manufacturing process. These designs are crucial for:
- Ensuring that parts meet specific dimensions and tolerances.
- Providing a clear outline for CNC (Computer Numerical Control) programming.
- Facilitating communication between clients and manufacturers.
2. Material Selection
Choosing the right material is fundamental in a lathe parts factory. Common materials used include:
- Aluminum: Lightweight and corrosion-resistant.
- Steel: Offers high strength and durability.
- Brass: Excellent machinability and aesthetic appeal.
- Plastic: Used for lightweight and non-corrosive applications.
The selection depends on the application requirements, such as strength, weight, and resistance to wear or corrosion.
3. Precision Machining
Once the materials are ready, the next phase involves precision machining. Techniques include:
- Turning: A primary function of lathes where material is removed from a rotating workpiece.
- Milling: Used to produce rectangular slots or complex shapes.
- Drilling: Creating holes at predetermined locations and dimensions.
Modern lathe parts factories utilize advanced CNC machines that offer high precision and can run automated processes for increased efficiency.
Quality Control: Ensuring Precision and Reliability
Quality assurance is a cornerstone of a lathe parts factory. Several tests and measures ensure that parts meet industry standards:
- Dimensional Inspection: Verifying that parts conform to specified dimensions.
- Material Testing: Assessing the mechanical properties of materials used.
- Functional Testing: Ensuring parts perform as intended in real-life applications.
These rigorous processes build trust with clients and maintain a factory's reputation in the competitive landscape.
The Economic Impact of Lathe Parts Factories
Lathe parts factories significantly contribute to the economy. They create numerous job opportunities, from engineers and programmers to machine operators and logistics coordinators. The ripple effects of their operations impact other sectors, including:
- Aerospace: Supplying critical parts for aircraft manufacturing.
- Automotive: Providing components for vehicles, enhancing safety and performance.
- Medical: Manufacturing precision parts for medical devices and equipment.
Moreover, the technological innovations spurred by these factories contribute to overall industry advancements, increasing production capabilities and efficiencies.
Technological Advancements in Lathe Parts Manufacturing
In recent years, technology has advanced rapidly, transforming how lathe parts factories operate. Some notable advancements include:
1. Automation and Robotics
The integration of automation and robotics in lathe parts factories has revolutionized the manufacturing process. Automated systems can:
- Increase production rates.
- Reduce human error.
- Enhance safety by taking over dangerous tasks.
2. Advanced CNC Machines
Today's CNC machines are capable of handling complex programming and can operate multiple machines simultaneously. This leads to:
- Increased accuracy and repeatability.
- Reduced lead times for production.
- Better resource management and reduced waste.
3. Additive Manufacturing
While traditional lathe work is subtractive, additive manufacturing (3D printing) is gaining traction in producing components and parts. This method allows for:
- Rapid prototyping of new designs.
- Creation of complex geometries that would be challenging through traditional machining.
- Reduction in material waste due to precise material usage.
Environmental Considerations in Lathe Parts Factories
More than ever, businesses are recognizing the need to operate sustainably. Lathe parts factories are implementing practices to minimize their environmental impact:
- Waste Management: Segregating waste materials for recycling.
- Energy Efficiency: Utilizing machinery that consumes less energy and reduces emissions.
- Water Conservation: Implementing closed-loop systems for coolant and cleaning processes.
These proactive measures not only help the environment but also improve a factory’s marketability, as clients increasingly demand sustainability in their supply chains.
Choosing the Right Lathe Parts Factory
When selecting a lathe parts factory for your manufacturing needs, consider the following:
- Experience and Expertise: Look for a factory with a proven track record in your industry.
- Quality Assurance Standards: Ensure they have robust quality control measures in place.
- Technological Capability: Assess their machinery and technology to ensure they can meet your specifications.
- Customer Service: Good communication is vital; choose a factory that values client relationships.
Conclusion: The Future of Lathe Parts Factories
The role of a lathe parts factory is indispensable as we transition into an era of smart manufacturing and Industry 4.0. As technology continues to evolve, these factories will remain at the forefront, delivering precision-engineered parts that power our modern world. By investing in cutting-edge technology, committing to sustainability, and focusing on quality, lathe parts factories will continue to thrive and support various industries, making significant contributions to global manufacturing and innovation.
For businesses looking for exceptional quality and customized solutions, turning to a reliable lathe parts factory is not just a choice; it’s a sound investment in the future.
For more information about our services, visit deepmould.net.