Transforming Industry with High Pressure Die Casting Products
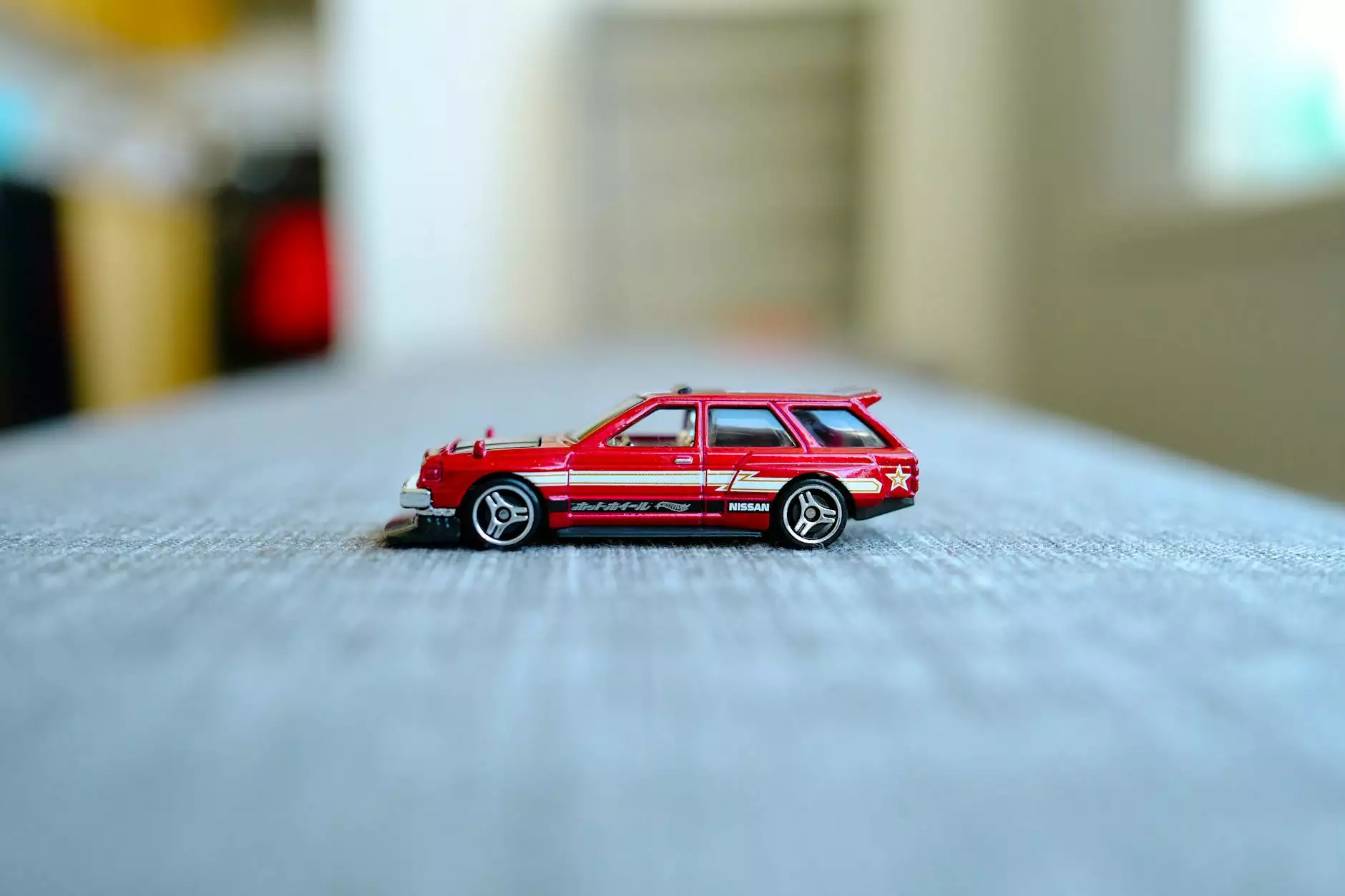
The industrial landscape is continually evolving, driven by the need for more efficient, durable, and cost-effective manufacturing solutions. At the forefront of this transformation are high pressure die casting products. This article delves into the significance of these products, their myriad applications, and why they are pivotal in the modern manufacturing ecosystem. We will also highlight how Deep Mould, a leading entity in the metal fabrication sector, excels in delivering these products.
Understanding High Pressure Die Casting
High pressure die casting (HPDC) is a manufacturing process that utilizes high-pressure injection of molten metal into a steel die, resulting in precision-engineered products. This method is particularly suited to metals such as aluminum, zinc, and magnesium, which allow for efficient molding and finishing.
The Process of High Pressure Die Casting
The HPDC process can be broken down into several critical phases:
- Preparation: The die must be prepared and pre-heated to the optimum temperature, ensuring the molten metal flows smoothly.
- Injection: The molten metal is injected into the die at high pressure, which enables detailed shapes to be formed with rapid cooling.
- Cooling: Once injected, the metal cools and solidifies quickly, usually within seconds.
- Ejection: After cooling, the die is opened, and the cast product is ejected, ready for secondary finishing processes.
Advantages of High Pressure Die Casting
High pressure die casting offers several distinct advantages, which makes it a preferred choice for manufacturers:
- High Precision: The HPDC process results in intricate designs with tight tolerances, making it ideal for complex geometries.
- Rapid Production: This method allows for high-volume production, significantly reducing cycle times and enhancing efficiency.
- Superior Surface Finish: Components produced through HPDC often require minimal surface finishing, saving time and cost.
- Cost-Effectiveness: High pressure die casting is economical for large batches, reducing material waste and manufacturing costs.
Applications of High Pressure Die Casting Products
The versatility of high pressure die casting products extends across multiple industries, thanks to their inherent strengths:
Aerospace Industry
In aerospace, components must meet stringent safety and performance standards. HPDC products such as aircraft brackets and housings provide the required strength-to-weight ratio. By utilizing high-quality aluminum alloys, manufacturers can ensure durability while maintaining a lightweight structure.
Automotive Sector
The automotive industry heavily relies on HPDC for producing parts like engine blocks, transmission cases, and structural components. The ability to cast complex shapes reduces assembly time and enhances overall performance. Additionally, lightweight HPDC components contribute to fuel efficiency.
Electronics
In the electronics sector, high pressure die casting is used for making enclosures and housings for devices. The thermal conductivity of the metal ensures optimal heat dissipation, safeguarding electronic components from overheating.
Consumer Goods
Everyday products such as kitchen appliances or tools often integrate components manufactured through HPDC, combining efficiency with aesthetic appeal. These products benefit from the process's ability to produce high-quality finishes and intricate designs.
Deep Mould: Your Partner in High Pressure Die Casting
At Deep Mould, we pride ourselves on our expertise in producing high pressure die casting products that meet the highest standards of quality and precision. Our commitment to utilizing cutting-edge technology ensures that we stay competitive in the rapidly changing market.
Quality Assurance Practices
We implement rigorous quality control measures throughout the production process. This includes:
- Material Inspection: All raw materials undergo thorough testing to ensure they meet specified standards before production.
- In-Process Quality Checks: Our engineers conduct real-time monitoring during the casting process to detect and rectify any anomalies.
- Final Product Testing: After production, each product is meticulously inspected to guarantee conformity to design specifications.
Innovative Solutions and Customization
Understanding that every client has unique requirements, Deep Mould offers tailored solutions in high pressure die casting. Whether you require a specific alloy, size, or surface finish, our team collaborates closely with you to deliver customized products that perfectly fit your application.
Sustainability and Environmental Responsibility
In today’s market, sustainability is more critical than ever. At Deep Mould, we are committed to environmentally responsible practices, including:
- Recycling Metal Waste: Minimizing waste through effective recycling strategies.
- Energy Efficiency: Investing in energy-efficient machinery and processes to reduce our carbon footprint.
- Compliance: Adhering to all relevant environmental regulations and striving to exceed them.
The Future of High Pressure Die Casting
The future of high pressure die casting products looks promising. As industries continue to advance, the demand for precision-engineered components will grow. Innovations such as 3D printing technology, improved alloys, and enhanced automated processes are expected to revolutionize the industry, offering even greater efficiency and capability.
Emerging Technologies to Watch
Several trends and technologies are set to impact high pressure die casting in the coming years:
- Automation: The integration of robotics and AI in production lines will further enhance efficiency and consistency.
- Additive Manufacturing: Combining HPDC with 3D printing techniques could lead to hybrid processes that leverage the benefits of both technologies.
- Smart Manufacturing: The Internet of Things (IoT) will enable real-time monitoring and data analytics, optimizing production workflows.
Conclusion
High pressure die casting products are indispensable in modern manufacturing, driving innovation across various industries. From the automotive to aerospace, the benefits of HPDC are vast, offering unparalleled precision and efficiency. With Deep Mould at the helm of this technology, businesses can confidently navigate their production challenges, armed with the knowledge that they are receiving the best high pressure die casting solutions available.
As we look to the future, embracing emerging technologies and sustainable practices will ensure that high pressure die casting continues to evolve and thrive, meeting the demands of an ever-growing market.